BUSINESS
2024 Maintenance Tech Progression 06.25.2024.pdf: The Future of Predictive Maintenance
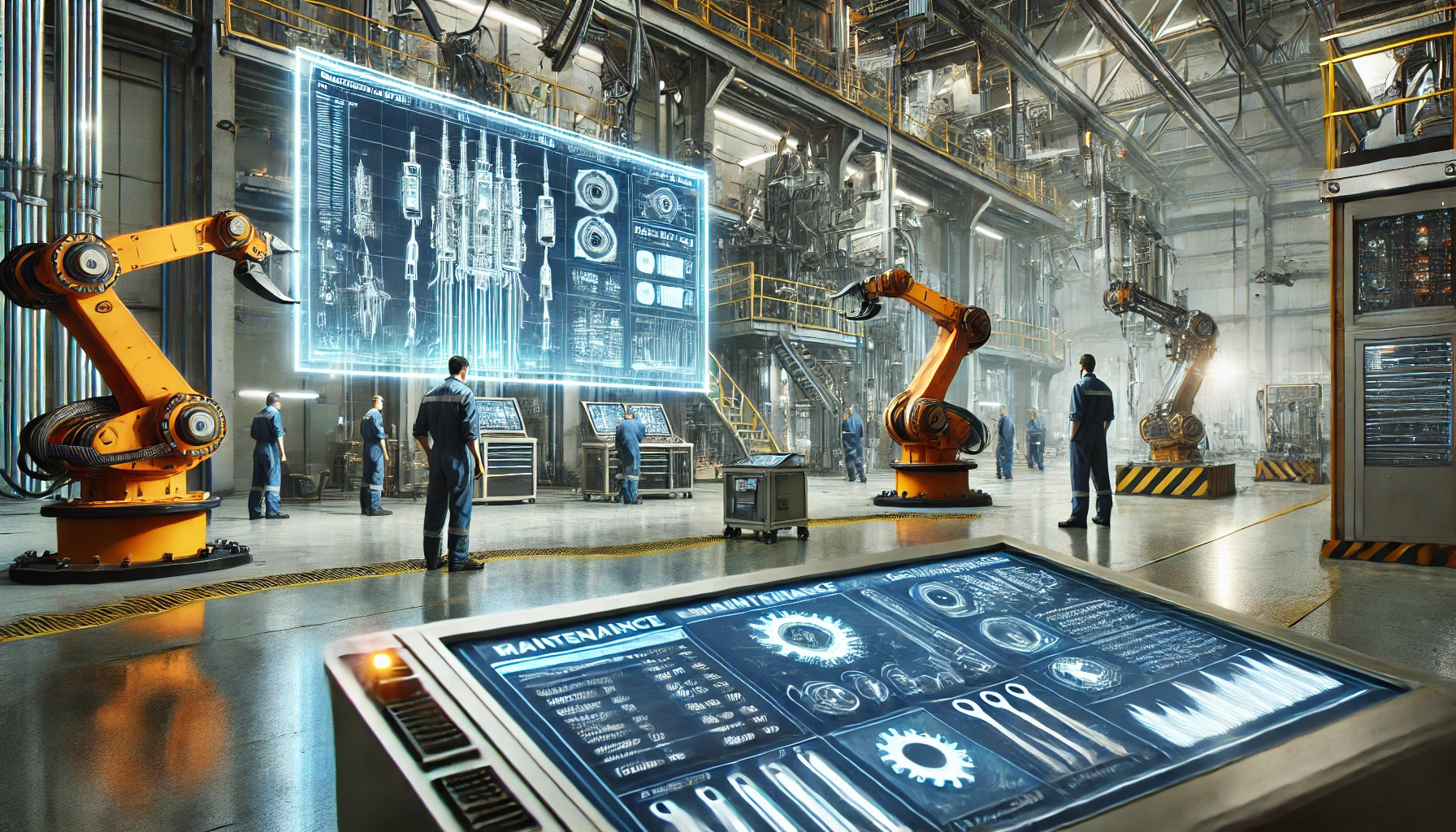
Maintenance technology is evolving rapidly, transforming industries such as manufacturing, energy, transportation, and facility management. Companies must embrace smart maintenance solutions to enhance efficiency, minimize downtime, and reduce costs. The “2024 Maintenance Tech Progression 06.25.2024.pdf” provides valuable insights into the latest advancements in maintenance technology and how businesses can leverage them for sustainable growth.
Understanding the Importance of Modern Maintenance Technology
Industries rely on well-maintained equipment to ensure smooth operations. Traditional maintenance strategies often led to unexpected failures, high repair costs, and extended downtimes. However, with advancements in predictive analytics, IoT-enabled monitoring, and automation, businesses can now implement proactive maintenance strategies to prevent breakdowns before they occur.
Key Benefits of Advanced Maintenance Technologies
- Increased Equipment Lifespan: Early detection of faults reduces wear and tear.
- Reduced Downtime: Predictive analytics minimizes unexpected failures.
- Cost Savings: Automated monitoring eliminates unnecessary maintenance costs.
- Enhanced Safety: Smart sensors prevent hazardous failures in critical industries.
- Sustainability: Energy-efficient maintenance reduces environmental impact.
Key Trends in Maintenance Technology for 2024
The “2024 Maintenance Tech Progression 06.25.2024.pdf” highlights several cutting-edge trends shaping the future of maintenance:
Predictive Maintenance (PdM) Using AI & Machine Learning
- AI-driven algorithms analyze data patterns to predict equipment failures before they happen.
- Reduces the need for manual inspections and increases efficiency.
- Helps industries shift from reactive to proactive maintenance.
IoT-Enabled Smart Sensors for Real-Time Monitoring
- Sensors track temperature, pressure, vibration, and other parameters to detect anomalies.
- Cloud-based platforms provide instant alerts for potential issues.
- Ensures continuous equipment performance monitoring without human intervention.
Digital Twin Technology for Maintenance Optimization
- Virtual replicas of physical assets simulate equipment performance.
- Engineers can test maintenance strategies before applying them in real-world scenarios.
- Improves decision-making and reduces costly trial-and-error methods.
Automated Maintenance & Robotics
- AI-powered maintenance robots perform inspections and minor repairs.
- Drones and automated systems monitor remote and hazardous locations.
- Reduces human errors and enhances maintenance precision.
Cloud-Based Maintenance Management Systems (CMMS)
- Centralized platforms for storing maintenance logs, schedules, and asset data.
- Allows remote access to maintenance insights across multiple locations.
- Facilitates collaboration between teams for more efficient maintenance planning.
How Businesses Can Implement These Technologies
For businesses to benefit from these advanced maintenance technologies, they must take a strategic approach to implementation. The “2024 Maintenance Tech Progression 06.25.2024.pdf” suggests the following steps:
Assess Current Maintenance Challenges
- Identify common equipment failures and inefficiencies in existing maintenance strategies.
- Analyze maintenance costs and unplanned downtime occurrences.
Invest in Predictive Maintenance Tools
- Deploy AI-powered maintenance software to analyze equipment health.
- Train employees to use smart diagnostic tools and data analytics platforms.
Upgrade to IoT-Based Monitoring Systems
- Install real-time sensors on critical machinery.
- Ensure data integration with cloud-based maintenance management systems.
Implement Digital Twin Simulations
- Create virtual models of high-value equipment to test maintenance strategies.
- Use simulations to predict the impact of different maintenance schedules.
Automate Maintenance Tasks Where Possible
- Deploy robotic inspectors for high-risk environments.
- Utilize automated maintenance logs to reduce manual paperwork.
Train Maintenance Teams on Emerging Technologies
- Conduct workshops on AI, IoT, and data analytics in maintenance.
- Encourage employees to adopt data-driven decision-making.
Future Prospects of Maintenance Technology
The future of maintenance technology is driven by further automation, enhanced AI capabilities, and seamless integration of digital tools. The “2024 Maintenance Tech Progression 06.25.2024.pdf” outlines the following emerging innovations:
Edge Computing for Faster Data Processing
- Reduces reliance on cloud processing by analyzing data at the device level.
- Improves response time for critical maintenance alerts.
Blockchain for Secure Maintenance Records
- Ensures tamper-proof maintenance logs for compliance and auditing.
- Provides transparent tracking of equipment lifecycle and repairs.
5G Connectivity for Instantaneous Monitoring
- Enables real-time communication between sensors, AI models, and operators.
- Facilitates seamless remote maintenance support.
Augmented Reality (AR) for Maintenance Training
- Technicians can visualize complex machinery in AR simulations.
- Reduces training time and improves on-the-job learning efficiency.
Conclusion
The “2024 Maintenance Tech Progression 06.25.2024.pdf” is an essential resource for businesses looking to stay ahead in the competitive industrial landscape. Predictive maintenance, IoT-based monitoring, AI-powered analytics, and automation are transforming how companies approach maintenance, leading to cost savings, improved efficiency, and reduced downtime.
By adopting these cutting-edge technologies, businesses can future-proof their maintenance strategies and ensure seamless operations in an increasingly digital and automated world.
FAQs
What is the main focus of the 2024 Maintenance Tech Progression?
It highlights advancements in predictive maintenance, IoT monitoring, AI-driven analytics, and automation for efficient equipment management.
How does predictive maintenance benefit industries?
It prevents unexpected breakdowns, reduces downtime, and lowers maintenance costs by detecting issues before failure occurs.
What role does IoT play in modern maintenance technology?
IoT enables real-time equipment monitoring through smart sensors, ensuring proactive maintenance and optimized performance.
How can businesses implement these new maintenance technologies?
Companies should adopt AI-based diagnostics, IoT sensors, digital twins, and automation while training employees for effective use.
What are the future trends in maintenance technology?
Key trends include edge computing for faster data processing, blockchain for secure records, 5G connectivity, and AR-based training.
BUSINESS
Heavy Equipment Overhaul Checklist
Many heavy machinery operators start to worry when they hear that the machine needs to be overhauled in the factory. This is not only because of the delay in the construction period, but also because they are afraid that they will not be able to repair it after spending a lot of money. In fact, the overhaul itself is not terrible. What is terrible is that you have no idea about the machine, are not familiar with the process, and have no idea about the parts that need to be prepared. No matter how professional the repair shop is, you still need to cooperate with them to prepare the parts, otherwise, you will have to swallow the time and cost.
List of Key Parts
Before sending the equipment for repair, the best situation is to make a preliminary judgment on which systems may have problems based on the abnormal performance during use, such as slow start, insufficient power, weak hydraulic pressure, and soaring fuel consumption. The engine, hydraulic system, cooling system, and transmission system are the hardest hit areas during an overhaul. Common parts that need to be replaced include the oil filter, fuel filter, hydraulic oil filter, seal, water tank hose, belt, intake and exhaust valve, fuel injector, piston ring, starter motor, and various sensors.
Taking CASE equipment as an example, it is usually necessary to check and replace the filter, seal kit, and operating valve of the hydraulic system during overhaul, and it may also involve the internal parts of the gearbox and the electronic control module. At this time, choosing the right CASE parts is particularly critical – it is not only related to whether the equipment will run smoothly in the future, but also directly affects the maintenance cost and cycle. If you prepare suitable original or high-quality replacement parts in advance, it will not only save waiting time, but also avoid repeated repairs due to parts problems.
Different Replacement Parts for Different Equipment
Equipment is not getting more and more useless as it gets older, but as the service life of the equipment increases, the demand for the quality of parts will indeed become higher and higher. If the service life of your equipment is less than 3 years, it is basically based on routine maintenance. Replacement of consumables such as filters, belts, and hydraulic oil can mostly restore the status.
After about 3-6 years, it is recommended to start paying attention to the deep components of the hydraulic system and fuel system, such as the pump body, fuel injector, and pressure sensor, because at this time, many problems begin to change from “abnormal performance” to “functional decline”. If the equipment has been used for more than 6 years, it is recommended that you prepare more key assemblies in advance, such as turbochargers, gearbox components, and electronic control circuit modules. This type of old machine may seem to work normally, but it is easy to break down when working on-site with high intensity. Replacing the problematic parts in advance is the real peace of mind.
Choose the Right Shopping Platform
In addition to saving time, there is a core logic for preparing spare parts in advance: a reliable parts platform can make you feel at ease when repairing. You have to consider: Is the model of the parts accurate? Are there any physical pictures and comparison information? Does it support one-click search by equipment model? These seemingly “e-commerce functions” actually directly affect whether you can buy the right one and install it at one time. Friday Parts allows equipment owners to purchase for themselves. The parts list is clear, supports searching by model, and can also check the original factory number of replacement parts. Whether you use CASE, Caterpillar, John Deere, or Hitachi, you can quickly match them.
Conclusion
Many people are used to not going to the site for an overhaul until the equipment “cannot be operated”, but this is actually unnecessary. You can refer to the equipment maintenance cycle to plan in advance, or start recording abnormalities when minor faults occur. Once you find that the problems occur in batches, it is time to prepare. Make a list of accessories in advance, and start working directly as soon as the equipment arrives at the factory, which can save a week of delay. Don’t underestimate the difference of these few days – in the peak season, it means you can take on more orders and make more money.
BUSINESS
Apex Traffic vs ClickSEO: How to Use Both for Instant and Long-Term Website Success
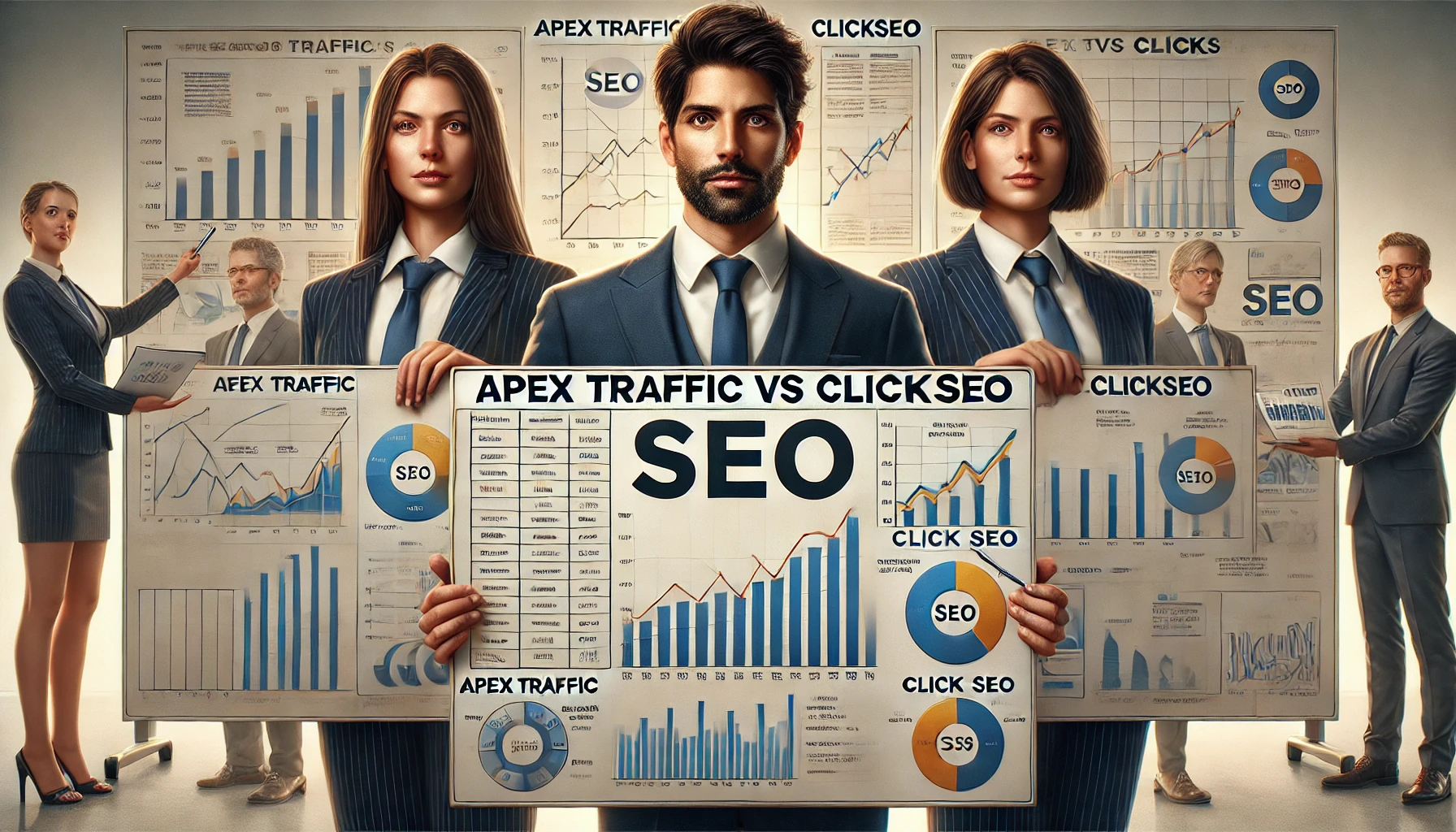
Every online business needs visitors, but how do you get them? Two popular strategies are Apex Traffic and ClickSEO. Each has a different approach, and choosing the right one depends on your business goals.
Apex Traffic brings instant visitors through paid advertising. It is a great option when you need quick exposure. However, it requires continuous investment.
ClickSEO, on the other hand, focuses on organic search engine rankings. It helps businesses grow in the long run by improving website visibility on Google and other search engines.
In this article, we will explore the key differences, benefits, and when to use each method. Understanding Apex Traffic vs. ClickSEO will help you make an informed decision for your business.
What is Apex Traffic?
Apex Traffic is a strategy that relies on paid ads to drive visitors to a website. This means businesses pay for clicks, impressions, or conversions. Popular platforms include Google Ads, Facebook Ads, and Instagram Ads.
One of the biggest advantages of Apex Traffic is its immediate impact. As soon as the campaign goes live, traffic starts coming in. This makes it perfect for new product launches or time-sensitive promotions.
However, it requires a continuous budget. Once the ads stop, the traffic disappears. Businesses must keep investing to maintain a steady stream of visitors.
Apex Traffic is highly targeted. Ads can be customized based on audience demographics, interests, and behaviors, ensuring they reach the right people.
What is ClickSEO?
ClickSEO focuses on improving a website’s organic search ranking. It involves optimizing content, using relevant keywords, and building quality backlinks to increase visibility.
Unlike Apex Traffic, ClickSEO does not provide instant results. It takes time to build authority and climb search rankings. However, once a site ranks well, traffic continues without additional costs.
SEO is a long-term investment. While it may take months to see results, the benefits are lasting. A well-optimized website can generate free traffic for years.
Another advantage of ClickSEO is trust and credibility. Users often trust organic search results more than paid ads, leading to higher engagement and conversion rates.
Key Differences Between Apex Traffic and ClickSEO
Both methods drive traffic, but they work in different ways. The table below highlights the main differences:
Feature | Apex Traffic | ClickSEO |
Speed of Results | Immediate | Slow (Months) |
Cost Structure | Continuous Spending | One-time Investment |
Sustainability | Short-Term | Long-Term |
Trust & Credibility | Lower (Ads) | Higher (Organic) |
Traffic Control | Full Control | Dependent on Search Engine Updates |
Apex Traffic is best for businesses that need fast results, while ClickSEO is ideal for those looking for consistent, long-term traffic.
Businesses with a limited budget may prefer ClickSEO, as it does not require constant spending. However, Apex Traffic is useful for launching a brand or testing new products.
Pros and Cons of Each Strategy
Both Apex Traffic and ClickSEO have their strengths and weaknesses. The right choice depends on business needs and goals.
Apex Traffic Pros
- Instant traffic boost – great for new products or seasonal offers.
- Precise audience targeting – ads can be customized to reach the right people.
- Predictable results – traffic is directly linked to ad spend.
Apex Traffic Cons
- High cost – continuous investment is required.
- No lasting impact – traffic stops when ads stop.
- Lower trust factor – many users ignore ads.
ClickSEO Pros
- Free and sustainable traffic – no need to pay for every visitor.
- Builds authority and trust – organic results are preferred by users.
- Long-term ROI – once ranked, traffic remains consistent.
ClickSEO Cons
- Takes time – months of effort before seeing results.
- Requires ongoing optimization – Google algorithms frequently change.
- Competitive – high-ranking keywords can be difficult to achieve.
When Should You Use Apex Traffic?
Apex Traffic is best when businesses need fast and predictable results. It is useful in situations where speed matters.
If you are launching a new product or service, paid ads can quickly create awareness. This is especially useful for e-commerce brands.
Seasonal promotions, such as holiday sales or Black Friday discounts, benefit from Apex Traffic. Ads can drive visitors who are actively looking to buy.
Businesses testing new markets or audiences should consider Apex Traffic. Paid ads provide immediate feedback on what works and what doesn’t.
If your goal is fast lead generation, Apex Traffic ensures a steady stream of potential customers. This is useful for real estate, finance, or high-ticket sales industries.
When Should You Use ClickSEO?
ClickSEO is the right choice for businesses looking for long-term growth. It works well for companies that want steady, sustainable traffic.
If you are building a brand, SEO helps establish credibility. A website with high search rankings gains trust from users.
For businesses with a limited marketing budget, ClickSEO is ideal. Once rankings improve, traffic comes in without additional costs.
Companies focusing on content marketing should prioritize SEO. Writing blogs, guides, and FAQs helps websites rank for multiple keywords.
If your goal is higher conversion rates, SEO traffic often performs better. Organic visitors are usually more interested in the content they find.
The Best Strategy – Should You Combine Both?
Many businesses use a hybrid approach, combining Apex Traffic and ClickSEO. This ensures both short-term and long-term success.
Apex Traffic can be used to gain immediate exposure, while SEO works in the background to build authority. This way, businesses get the best of both worlds.
One strategy is to run paid ads for important keywords while waiting for SEO to improve rankings. Once organic traffic increases, reliance on ads can decrease.
For startups and small businesses, a balance of 60% SEO and 40% paid ads can provide both stability and growth. This allows businesses to scale efficiently.
Using both strategies maximizes ROI. Businesses benefit from fast traffic from ads and long-term free traffic from SEO.
Conclusion
Choosing between Apex Traffic vs. ClickSEO depends on your business goals, budget, and timeline. Each method has its unique advantages.
Apex Traffic is great for quick results, but it requires ongoing spending. ClickSEO takes longer, but it provides sustainable growth without continuous ad costs.
For most businesses, a combination of both strategies works best. Paid ads help in the short term, while SEO builds lasting success.
By understanding the key differences, businesses can make smarter decisions to drive traffic and grow online.
FAQs
Which is better for a new business, Apex Traffic or ClickSEO?
Apex Traffic is better for instant visibility, while ClickSEO is ideal for long-term brand growth. A combination of both works best.
Does Apex Traffic guarantee sales and conversions?
No, Apex Traffic brings visitors quickly, but conversions depend on factors like ad quality, landing pages, and product appeal.
How long does it take for ClickSEO to show results?
SEO usually takes 3 to 6 months to see noticeable improvements, but once ranked, traffic remains consistent without extra costs.
Can I stop using Apex Traffic once ClickSEO improves?
Yes, but some businesses keep running low-cost paid ads for additional exposure while relying on organic SEO for free traffic.
Is ClickSEO completely free?
SEO traffic is free, but it requires investment in content creation, backlinks, and optimization to achieve higher rankings.
CRYPTO
Crypto30x.com Zeus: The Ultimate AI-Powered Trading Bot for Smarter Cryptocurrency Investments
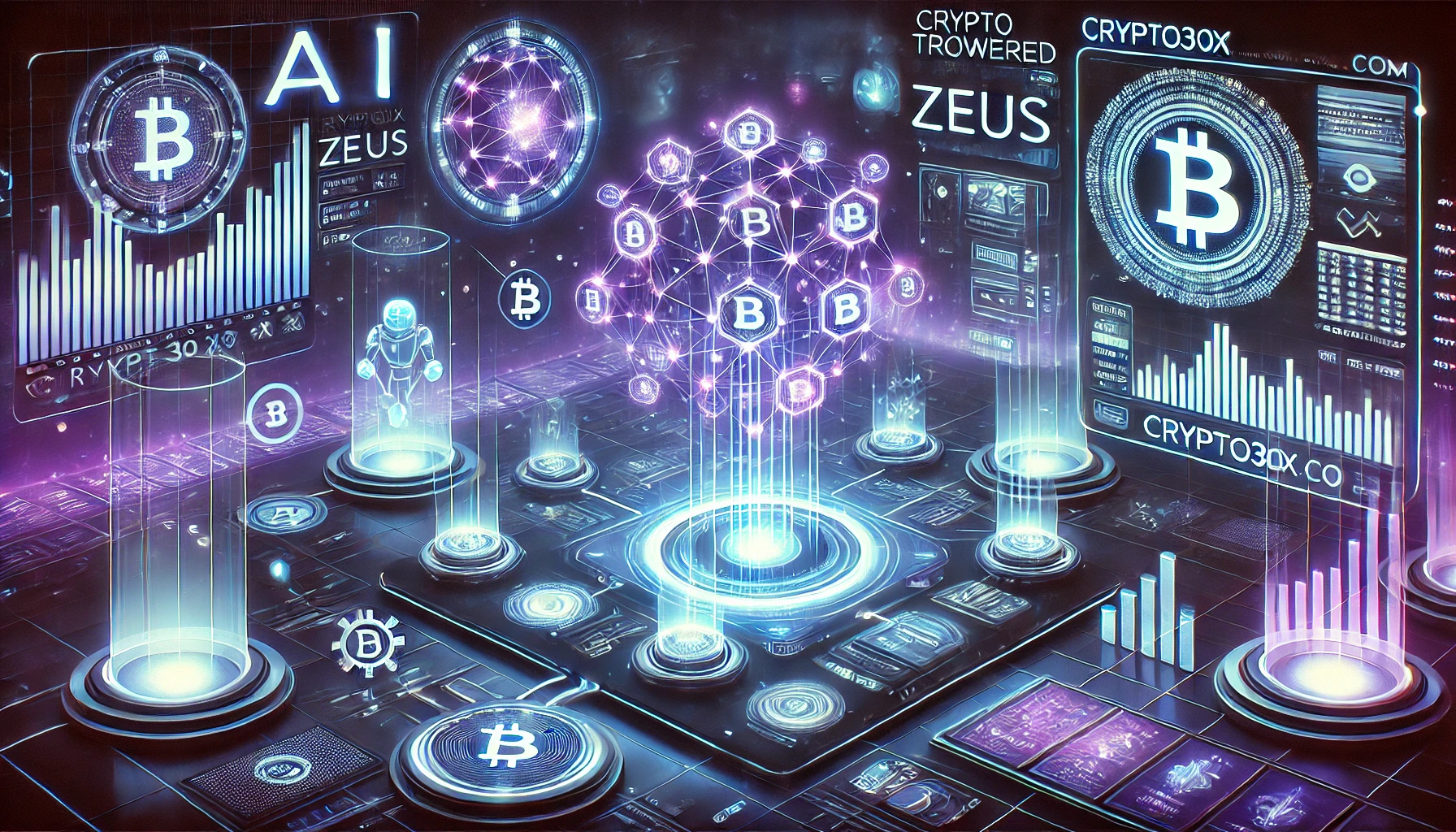
Crypto30x.com Zeus is an advanced AI-powered cryptocurrency trading platform that automates the trading process. It allows users to trade efficiently without constantly monitoring the market.
The platform is designed to help both beginners and experienced traders optimize their investments. By using automation, it removes emotional decision-making and executes trades with precision.
Artificial intelligence and machine learning play a crucial role in analyzing market patterns. Crypto30x.com Zeus scans historical data, real-time market trends, and trading volumes to make data-driven decisions.
As cryptocurrency markets operate 24/7, manual traders often struggle to keep up. With automated systems like crypto30x.com zeus, users can trade continuously without missing opportunities.
Crypto30x.com Zeus: The Future of AI-Powered Crypto Trading
Crypto30x.com Zeus is a cutting-edge AI-driven cryptocurrency trading platform designed to automate trading and maximize efficiency. It helps traders execute profitable trades without the need for constant market monitoring. By leveraging machine learning and real-time data analysis, the platform predicts market trends and makes split-second decisions that human traders might miss.
One of the standout features of crypto30x.com zeus is its intelligent risk management system. It includes stop-loss, take-profit orders, and customizable strategies, allowing traders to control their risk levels. The platform operates 24/7, ensuring no trading opportunity is missed. Whether you’re a beginner looking for hands-off trading or an expert aiming to refine your strategies, crypto30x.com zeus offers an innovative solution for smarter, more efficient crypto trading.
How Crypto30x.com Zeus Works
Crypto30x.com Zeus operates on an AI-driven algorithm that continuously analyzes market fluctuations. The platform executes trades based on set conditions, eliminating the need for human intervention.
It gathers real-time market data from multiple sources and identifies profitable opportunities. The AI adjusts strategies dynamically to maximize potential gains.
The trading system follows a structured “Buy Low, Sell High” approach. However, it also incorporates risk management features like stop-loss orders to minimize losses in unpredictable markets.
One of its key advantages is the speed of trade execution. AI reacts instantly to market conditions, reducing delays that manual traders often face.
Key Features of Crypto30x.com Zeus:
- Automated trading with AI-driven strategies
- Live market monitoring for real-time decision-making
- Stop-loss & take-profit orders for risk control
- Customizable trading settings for different risk appetites
Key Features of Crypto30x.com Zeus
Crypto30x.com Zeus offers multiple trading tools that help users execute strategies efficiently. These tools ensure automation, accuracy, and better trade execution.
The platform includes AI-powered bots that operate on pre-defined algorithms. Users can set parameters to let the system trade on their behalf, even while they sleep.
A real-time market scanner tracks price fluctuations, identifying high-potential buy and sell points. This ensures traders stay ahead of sudden market shifts.
Another crucial feature is risk management. The system implements stop-loss and take-profit features to protect investments and avoid excessive losses.
Feature | Crypto30x.com Zeus | Traditional Trading |
Automated AI Trading | Yes | No |
24/7 Market Monitoring | Yes | No |
Customizable Strategies | Yes | Limited |
Risk Management Tools | Yes | Basic |
Fast Execution Speed | Yes | Slower |
Benefits of Using Crypto30x.com Zeus
Using crypto30x.com zeus offers several advantages over manual trading. One of the biggest benefits is time efficiency—traders no longer need to monitor charts all day.
AI-driven trading ensures emotion-free decision-making. Fear and greed often lead to poor trading choices, but automation removes these psychological factors.
Speed is another significant benefit. Since crypto markets are highly volatile, fast execution of trades can mean the difference between profit and loss.
The platform is user-friendly, making it accessible for both beginners and advanced traders. Users can customize their strategies, adjusting settings based on their risk tolerance.
Potential Risks & Considerations
Although crypto30x.com zeus provides automation, no system can guarantee profits due to the volatility of cryptocurrency markets. AI can predict trends but is not immune to sudden market crashes.
New users might face a learning curve when setting up their trading strategies. While automation simplifies trading, understanding the platform’s settings is essential.
There is always a risk of technical failures. A system glitch or internet disruption could lead to missed trades, impacting potential profits.
Over-reliance on AI can be risky. Traders should regularly review performance reports to adjust strategies and optimize results.
Key Considerations Before Using Crypto30x.com Zeus:
- Cryptocurrency markets remain unpredictable
- AI-based trading requires initial setup & strategy testing
- No platform can fully eliminate risks
How to Get Started with Crypto30x.com Zeus
To begin using crypto30x.com zeus, traders must first sign up on the platform and complete a simple registration process. KYC verification is required for security purposes.
After signing up, users deposit funds into their accounts. The platform supports multiple cryptocurrencies, allowing flexible funding options.
The next step is to customize trading preferences. Users can set risk levels, trade size, and preferred trading pairs before activating the AI trading bot.
Once everything is set up, traders can enable automated trading. The system will start executing trades based on the chosen strategy, allowing users to monitor performance.
User Experiences & Success Stories
Many traders have successfully used crypto30x.com zeus to optimize their investments. The platform has helped both beginners and experienced traders manage risk effectively.
For instance, a new trader who struggled with manual trading saw consistent profits after switching to AI-based strategies. Automation helped eliminate human errors and impulsive trading.
Another experienced investor used crypto30x.com zeus to enhance his portfolio by diversifying across different cryptocurrencies. AI’s market analysis provided insights that manual research would have missed.
A frequent issue among traders is panic selling. Automated trading helped a user avoid emotional decisions by sticking to a pre-planned strategy, resulting in steady growth over time.
Is Crypto30x.com Zeus Worth It?
Crypto30x.com Zeus is an excellent choice for traders looking to automate their strategies while maintaining control over risk management. Its AI-driven tools improve accuracy and execution speed.
The platform is particularly useful for busy traders who cannot monitor the market 24/7. It ensures they don’t miss out on profitable opportunities due to time constraints.
While AI trading offers efficiency, users should stay informed about market trends. Regularly checking trade reports and adjusting settings can improve long-term profitability.
Overall, crypto30x.com zeus provides a powerful solution for automated trading, but like any investment tool, it requires proper strategy and risk management.
Final Thoughts
Crypto30x.com Zeus is a powerful AI trading tool designed for efficiency and accuracy. By automating trades, it allows users to capitalize on market trends without constant monitoring.
While the platform provides numerous benefits, users should always remember that cryptocurrency trading carries risks. Learning and adjusting strategies is key to long-term success.
For traders looking for a smart and automated way to engage in crypto trading, crypto30x.com zeus is a solid option worth considering.
FAQs
How does Crypto30x.com Zeus make trading easier?
Crypto30x.com Zeus automates trading using AI, analyzing market trends and executing trades instantly without manual intervention.
Can I customize my trading strategies on Crypto30x.com Zeus?
Yes, users can set risk levels, trade size, and preferred strategies to match their investment goals.
Does Crypto30x.com Zeus guarantee profits?
No, while AI enhances trading efficiency, cryptocurrency markets remain volatile, and profits are not guaranteed.
Is Crypto30x.com Zeus safe from hacking risks?
The platform uses encryption, secure servers, and two-factor authentication to protect user accounts and funds.
Can I withdraw my funds anytime from Crypto30x.com Zeus?
Yes, withdrawals are allowed at any time, subject to the platform’s policies and processing times.
-
L,IFESTYLE1 year ago
Exploring the Heart of Iowa City Downtown District
-
SPORTS2 years ago
club america vs deportivo toluca f.c. timeline
-
CRYPTO2 years ago
Features of Liquidity Providers and Differences Between Them
-
TECH2 years ago
Maximizing Your Pixel 6a’s Wireless Charging Performance: Tips and Tricks
-
BUSINESS2 years ago
The Evolution of the Patagonia Logo: A Look at the Brand’s Iconic Emblem
-
TECH2 years ago
Build Your Email Marketing Contact
-
TECH3 years ago
6 Ways AI Will Change the Future of Marketing
-
CRYPTO2 years ago
The Essential Cryptocurrency Laws By State